54 Grit – J, wears quickly
Inexpensive
$12.00 - $15.00
54 Grit-J, good wheel
Mid-priced
$30.00 - $33.00
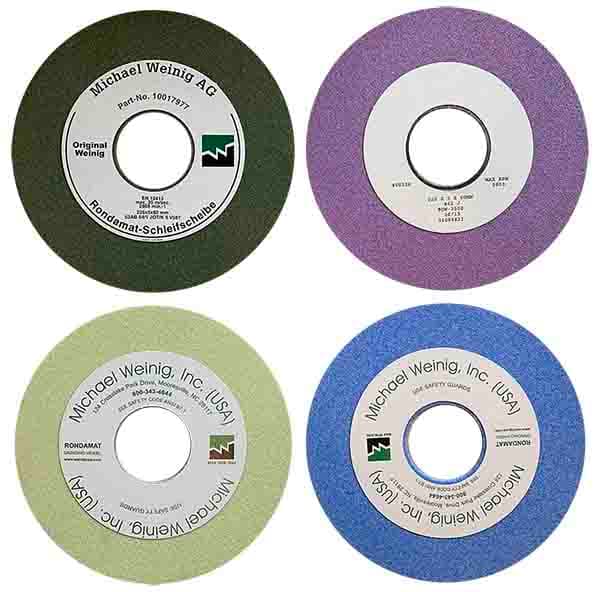
54 Grit-J, exceptional wheel (best-value)
Higher price range
$38.00 - $41.00
54 Grit-J, great wheel
Medium to high price
$32.00 – 35.00
What makes an abrasive wheel for grinding moulding knives more efficient than others that accomplish the same task? There are a few things you should know before purchasing any rough or finish wheel, like which product best suits your method of grinding knives, and the cost differences that might lean you toward a different type of abrasive wheel.
Grinding wheels are composed of a couple of objects, abrasive granules and glass bonding agent. These wheels contain thousands upon thousands of tiny granules, each of which have many cutting edges. Selecting a wheel with the correct abrasive granule type for your application can be difficult and confusing, in general the higher priced wheels listed above are the best value because of the way there manufactured. The best wheel for your application depends on the rate of which the steel can be removed, and its ability to constantly sharpen itself by granule fracturing and release without burning the knife steel.
Selecting the best grinding wheel for your application requires a good understanding of the composite of the wheel needed. A combination of abrasive type, grit size, hardness grade, granule structure, and bonding agent determines wheel performance. By varying the amount and type of each of these elements, the effectiveness of the wheel can be made to respond differently.
The abrasive granules are the elements of the grinding wheel that cuts the high-speed steel or carbide from the precut knife blanks . Here are a few abrasive types that we commonly use in our industry; aluminum, chromium and ceramic oxide, cubic boron nitride (CBN,) CDX, a combination of cbn and diamond for grinding inlay carbide where both the high-speed steel and inlay are ground simultaneously, and diamond specifically designed for solid tungsten carbide.
All abrasive granules are sized to an established worldwide standard and are designated as a numerical grit size, the larger the number, the smaller the granule size. Generally speaking a large number or coarse granules will increase stock removal rate but provide a poor surface quality finish. High number granule sizes provide less steel or carbide removal, but vastly improve surface finish quality. Most grinding wheel manufacturers utilize combinations of two or more grit sizes to produce various finishing effects for each grinding application.
Hardness grades for wheels are designated by a letter, A (softer) thru Z (harder). This letter grade represents the specific amount of bonding agent contained in the wheel which determines the ability to hold the abrasive granule in the wheel. Normally, the harder the grade the better surface quality you will obtain, but it provides a smaller chip removal rate than softer grades, which can lead to burning of the tool.
The grain structure of a grinding wheel refers to granule spacing within the wheel. This granule density is identified by a number from one thru sixteen. The more open composition within the wheel, the higher the number designated. A denser wheel will generally provide a better finish but will generate more heat with a slower metal removal rate than a more open structured wheel. So, to sum up what we have discussed so far, we recommend 54 - 60 grit wheels for roughing out the main portion of the moulding knife blank, and a 100 - 120 grit wheel for the micro finishing portion of the knife, this will provide a beautiful finished cut on the molding during the machining process.
The wheel bonding agent or binder is the material that holds the abrasive grain together. Here are a few essential properties of the best bonding agents. The binding agent must have the ability to retain the grain during grinding, self-sharpening and dressing applications. It must also retain the ability to allow the grain to be pulled out from the wheel when friction becomes high because the abrasive grain has become too dull to cut properly. Below are a few types of bonding agents that are common to our industry.
Vitrified - A glass bond characterized by its strength, rigidity, and resistance to oils, water, or temperature changes, like those used in our rough ceramic and finish CBN grinding wheels.
Resin - An organic bond used in grinding tools that offers rapid stock removal for finer finishes such as inlay and solid carbide, like those used in our cdx and diamond grinding wheels.
For the wood moulding industry, the most common grinding wheels used for manufacturing profile knives are made from either aluminum (white,) chromium (pink,) or ceramic (blue or green) oxide abrasives, and cubic born nitride (CBN) for finish grinding and putting the micro beveled edge on the cutting tip of the knives. Most professional profile grinder operators utilize a solid ceramic grinding wheel for rapid metal removal of high-speed steel, in combination with our 2mm, 125% concentration, 120 grit, 10mm of borazon for finish grinding. In fact, we nicknamed our custom designed wheel the “Mirror Reflections Ultimate Borazon Wheel” because of how smooth and precise the micro finish grinds are, the ability to hold the rounded edge to the end of the wheel life, and how long the wheel last, usually about one year of grinding eight to ten sets of profile knives per day.
Every change made within the elements of the wheel affects the way the wheel reacts during grinding procedures. Some other things must also be factored into the equation to determine the correct grinding wheel for your application, including the hardness of knife steel being ground, rpm speeds of the profile grinder being used and the grinding techniques of the individual operator.
Now you realize that proper grinding wheel selection and use can be confusing, hopefully we made it easier for you to decide what to purchase for your specific style in grinding molding knives. We have a large selection of grinding wheels for both rough and finish grinding moulder knives, located in both tooling catalogs under “Tooling & Supplies” tab on our website. We suggest you try a few different types of wheels to find the one that’s perfect for you. If we can be of any further assistance or have a specific question, feel free to contact us, we would be honored to help you.