Moulding Knife Template Design Video
This article will help explain how to determine what thickness, length and width of high speed steel you will need for cutting knife blanks in the production of custom moulding knives.
As most of you know, when milling wood mouldings it is very important to keep your cutting circles on every cutter head as small as possible. This practice allows you to close your moulder fences, bedplates, chip breakers and pressure shoe elements. Following these common practices on moulder or shaper setups allows the work piece to achieve the best possible support, thus virtually eliminating snipe or other finish problems.
High speed knife steel is available in many thicknesses and they all have their limitations. Here are a few examples of different thicknesses we supply, ¼” thick non-corrugated for Williams & Hussey and Shop Fox moulder's and 5/16” thickness corrugated knife steel for all other industrial machines. Each thickness of knife steel has its projection limitations, one quarter inch knife steel can be safely extended three quarters of an inch from the bottom of the gullet on the gib to the highest tip of the knife. The maximum depth of cut for Williams & Hussey or Shop Fox moulder is three quarters of an inch, (.750”). The most common thickness of knife steel is five sixteenths (.312”), this thickness of knife steel can safely extend one and one-half inches (1.500”) from the bottom of the gullet on the gib to the highest tip of the knife.
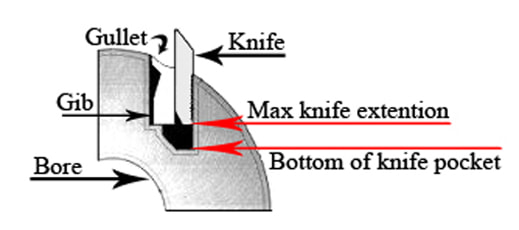
Let's talk about knife steel width, which is the height of knife steel bar. We strongly recommend having at least one bar of every width available in reserve if you manufacture your own molding knives. We have a wide range of every size available for your convenience. .
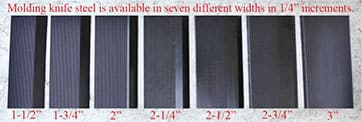
Here is a simple but effective way to determine which size width of knife steel you will need to manufacture your own knives. We use these calculations in all our cut steel sizes for moulding knife blanks listed on our approval sheets. They allow for some real benefits while milling lumber. First, it will enable the steel to sit deeply in the pockets in the cutter head; second, the blanks will be under full support of the gib. Finally, it allows the knives to be about one-quarter of an inch in height for sharpening before they reach the max knife extension safety limit marked on your cutter heads (see above image).
Depth of cut + 1-3/8” = width of steel, if you fall between widths of steel go to the next highest width available.
• Depth of Cut 0” thru 1/8” | = 1-1/2” wide (straight knives) |
• Depth of Cut 1/8” thru 3/8” | = 1-3/4” wide |
• Depth of Cut 3/8” thru 5/8” | = 2” wide |
• Depth of Cut 5/8” thru 7/8” | = 2-1/4” wide |
• Depth of Cut 7/8” thru 1-1/8” | = 2-1/2” wide |
• Depth of Cut 1-1/8” thru 1-3/8” | = 2-3/4” wide, Red Flag warning (some moulders will not swing this size) |
• Depth of Cut 1-3/8” thru 1-1/2” | = 3” wide, Red Flag warning (many moulders will not swing this size) |
If you use knife steel width that is too big or too small than recommended it will hinder your moulding operation one way or another.
Larger knife steel widths than recommended will make the life of the knife last longer, but you will sacrifice your small cutting circle to a larger one, this action will force you to open the bedplates and pressure shoe elements which will lead to snipe and other finish problems. Smaller knife steel widths than recommended will take you too close to the maximum knife extension zone on the cutter head and reduce the amount of times you will be able to sharpen the knife steel.
Last but certainly not the least; this is how to determine what length to cut the knife steel blank.
Width of finished moulding + ¾” = length of knife. Example 3” wide moulding plus ¾” = 3.750” (Top and bottom cutter heads)
Thickness of finished moulding + ¾” = length of knife. Example 1” thick moulding plus ¾” = 1.750” (Left and right cutter heads)
Here is the breakdown of why we use these dimensions, .394” of the .750” equation is reserved for the reference side (axial constant) and the remaining amount is on the opposite side of the knife, this will also add strength to the edges of the blades while milling.
For safety reasons there is a minimum size of 1.750” in length, we do not cut any piece of steel shorter, for safety purposes the knife steel must be under at least two gib screws in the cutter head. We use this default in all our molding knives to protect the machine operators, this default should be considered common practice when cutting blanks.
All moulding manufacturers that conduct business with Mirror Reflections know we always include the cut steel size on our detailed CAD drawings. We put a lot of vital and valuable information in our designs to help you better understand the milling process, save you valuable time, and help eliminate mistakes that could cause machining issues. Although it takes us a substantial amount of time to design a quality moulding, it is the foundation of the tool, which is a critical step to a superior designed acrylic template used to manufacture a quality moulding knife.
If you have any questions or need further assistance please feel free to contact us.