The topic of backout or relief cuts in wood mouldings is one of the more common questions summoned to answer. Questions come up from time to time on weather a certain wood moulding product requires a specific backout or not, my answer, more often than not, is generally yes.
A backout is plow or relief cut on the backside of a wooden moulding to help with cupping and or warping; it also allows for airflow between objects and provides a good transition between framing and sheet rock.
Backouts have a many purposes that in general people just do not give much thought to; they serve an important part of the manufacturing and installation process of many elegant wood mouldings. Technological advances in wood kiln drying techniques over the years has reduced the necessity for backouts whose foremost purpose was to relieve stress caused by case hardening in the lumber, most modern day wood kiln dried lumber have eliminated these issues.
Backouts can be made of various shapes and or sizes depending on the numerous moulding designs manufactured, some backout designs achieve superior results than others do, so a wide range of backout moulding knives are preferred by most moulding manufactures.
The list below provides some particular examples of backout applications and offers some motive for their use; they are in no specific order of importance.
- Backouts allow for airflow after moulding installation, in general one sixteenth to one eighth of an inch in height of backout for each three quarter to one inch of thickness of finished product. We prefer to use 45-degree angles in the transition areas, reason being, it will be easier to sharpen moulding knives when needed and moulding knives will benefit with longer manufacturing run times than that of backout designs that have transitions of greater angles.
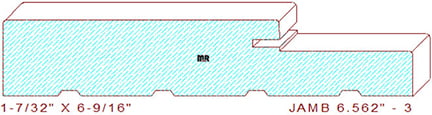
- Backouts assist in maintaining the lumber’s stability if the timber was improperly dried, resulting in case hardening cupping and or bowing of the work piece, as explained earlier, todays drying procedures are superior to days past but only if drying procedures are supported correctly.
- Milling backouts in baseboard and casing will aid in the transition between rough framing materials and sheet rock allowing the moulding to seat properly. Please maintain a sufficient distance from the edges of the moulding before the backout begins, this practice will aid in the elimination of the possibility of the moulding splitting when being nailed during installation process. Sometime construction adhesive used to install these types of mouldings could lead to unfavorable concerns; this backout area serves as an excellent space to apply the adhesive without interfering with the proper installation of said products.
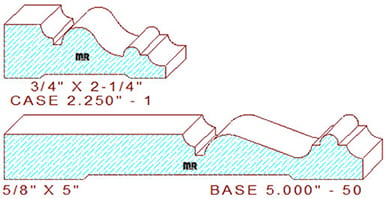
- Strategically placed flutes or half circles milled into the backs of crowns will make it easier for both the height and projection sides of the crown to seat properly during cutting and installing procedures; many crown designs have large depth of cuts, which leads to cupping causing the finish product to become out of square after milling. Back cutting the crown bevels by a half-degree or so will help these issues but also keep in mind they will change the overall height and projection of the crown moulding.
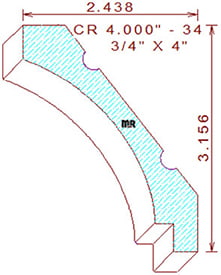
- Several moulding manufactures who manufacture more commonly used moulding profiles such as the WM series utilize the backout section of their particular mouldings for identification purposes. These identification marks can identify the month of production, the mill that manufactured it, shift in which manufactured, as well as the year manufactured; these back outs with identification marks eliminate the possibility fraud in the event of a return due to damage or any other concern that might need attention.
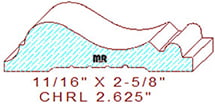
- Sometimes refraining from the use of backouts in wood mouldings is a necessity. Plinth blocks for example have ends exposed and a backout would make the end look unappealing, a hidden backout if possible would help the product remain stable after machining.
In conclusion, on the topic backouts in moulding profiles we trust we have enlightened your overall knowledge of the usage of different style backouts as well as their potential applications and benefits. If you would like to view a wide variety of over two hundred backouts we have in stock please visit our moulding profile catalog , if we can be of any further assistance please contact us.