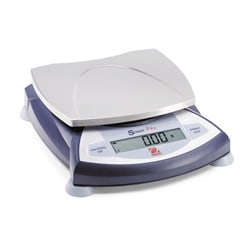
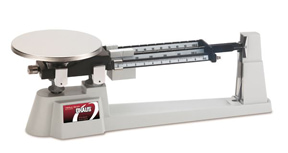
We want to share some information on the importance of balance scales for weighing high-speed steel and carbide profile knives and all your tooling before milling lumber on industrial machinery. For anyone to produce high-quality moldings (twenty to twenty-five knife marks per inch) knife marks per inch or more, it starts with a balanced weight of the cutter head, gibs, gib screws, and knives. Your company's reputation for producing premium wood profiles is on the line; please realize this is a critical task to take care of in your toolroom.
Every gram, a cutter head is out of balance between opposing sides; you retain twenty-two pounds of egg shape pressure on your spindle bearings per revolution. Most industrial moulding machines operate at spindles speeds between six thousand and twelve thousand revolutions per minute; it would be like banging the spindle bearings with a hammer. Our point is you will eventually ruin those bearings while distorting and increasing the bore tolerances in the cutter heads. When finish problems get noticed in your milled lumber (inconsistent knife marks) , you get forced to spend money on new tooling to correct the issues at hand. There are no spindle bearings on unique modern HSK molders, but they still have weight sensors and will not run if knives are out of balance.
Mirror Reflections consistently balance's every set of knives produced within 1/10 of a gram. Your company should also balance cutter head screws, gibs, and other critical items in your tool room that go on the machinery before milling. The cutter heads get weighed and balanced by the manufacturer or other reputable company offering these services. There is generally good evidence of balancing from drill hole marks in random areas on the cutter head. The correct balance scale is an inexpensive insurance plan for your company. It's not uncommon for one angular contact bearing to cost hundreds of dollars; spindle assemblies have up to four bearings on one shaft. Most industrial molders have at least five or six spindle assemblies. You can avoid costly mistakes of replacing bearings when the spindle is out of tolerance. Be sure to first check with the manufacturer on acceptable measurements. You should purchase the whole spindle assembly with bearings if you have unacceptable tolerances. We hope you're starting to add up the cost and realize the point we are trying to make.
If I were looking into buying the most accurate balance scale available, I would purchase a digital one. Digital scales are easier to read and take less time to balance your tooling over the mechanical triple beam scale. Good balance scales for the tool room will cost you between $350.00 and $500.00 depending on the brand name and the max weight they can measure. In general, the higher the weight range the scale can balance, the higher the cost. Purchase a scale capable of measuring at least two-thousand grams; not many knives will go over that weight unless you have a twelve-inch molder. Look into the Ohaus scales ; they have many weight ranges depending on what you want to weigh; their scales are very accurate and easy to use. We have Ohaus products available in our tooling catalogs located under the “Tooling and Supplies” tab. Please don't hesitate to contact us if you have a few questions or need any help ordering these scales.
One word of caution, these scales seem to do vanishing acts all on their own. Lock it up every night, or take the risk of your local drug dealer finding better ways to put your scale to use. 😊